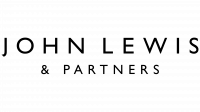
John Lewis Kitchens Reviews - johnlewis.com
Value For Money
John Lewis Kitchens Reviews - johnlewis.com
When you purchase through links on our site, we may earn an affiliate commission. Here's how it works.
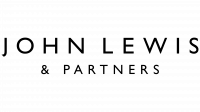
User Reviews
Value For Money
Unfinished And Starting To Fall Apart
My mother ordered her kitchen from John Lewis in 2022. It’s still not entirely complete, the finish of what has been installed is extremely poor (rough edges on worktops, gaps at the joins near the sink allowing water ingress, cupboards at the incorrect height, paintwork on the doors chipping and flaking already) and her complaints and requests for fixing the issues have fallen on deaf ears.
I am genuinely so shocked at this poor level of service and it has caused so much stress and upset to my parents.
Please avoid at all costs.
Value For Money
So Disappointing, Please Avoid At All Costs.
* John Lewis Fitted Kitchens ask top end prices but they sub-contract the work to unqualified builders (a very quick google search revealed that the 'vetted and checked' fitter was actually a bankrupt bricklayer
* Home and materials damaged by poor workmanship and sloppy attention to detail, the floor came up three times
* Extremely poor customer service from the case managers who are frequently out of the business but don't get their work covered or use the simplest of out-of-office auto-replies or accurate voicemail. No proactive service whatsoever, we spent HOURS chasing for information
* Every single delivery was problematic, either incomplete, the wrong colour or just non-existent
* A simply like-for-like refit was meant to take two weeks but was actually one day shy of 6 months
* Shamefully dismissive response from Head Office over our experience, a derisory goodwill gesture and no recourse for complaint. No accountability or responsibility taken even after verbally admitting it was a shambolic situation
* NOT part of a trade association and also refuses to take part in any sort of arbitration/ombudsman, this should tell you everything you need to know, I wish we'd realised before we parted with our money
I am interested to know more about your experience. We are having the exactly the same nightmare and have used someone of a similar description.
Very Poor Start With Jl Possibly A Sign Of Things To Come
I have spent several months researching kitchens and in the end decided on JL because I liked a particular range and it offered exactly the colours I was after. I also felt that JL would be a one-stop shop and that even if I was spending more, this and the JL name would ensure quality of product and services.
A planner paid a visit and a few days later sent a drawing plus some images. The design was, quite frankly, awful. It seemed like no thought or time had been spent on thinking it through. My requests to keep as much of the kitchen design as it currently is was not listened to and their plan contained: fewer cupboards, misaligned doors, and they admitted to their measurement of one wall being incorrect.
After receiving their design, I found myself wondering how and why on earth they'd come up with such a poor design that didn't maximise space, ignored my wishes and fundamentally detracted from many principals of good design.
I've contacted JL since twice to ask if I can start again with a different planner but no-one has come back to me.
Honestly, JL has recently posted huge losses and their CEO is leaving in '25, you'd have thought they'd do their best to keep hold of fitted kitchen customers who could easily be paying between £20-30,000, and deliver the best customer experience they can, but this does not seem to be the case. I've read the reviews below and while some seem to be written by competitors, I can see most are from genuinely aggrieved customers. I agree with many of them - from the few dealings I've had with JL fitted kitchens thus far, they seem disorganised with poor communication, and a distinct lack of customer care.
I'm sorely disappointed in JL. Such a poor service at the outset does not bode well for things going forward and I certainly don't want to find myself in similar stressful situations described below further down the line.
Value For Money
The Worst Customer Service Ever
Go somewhere else where they care! We went to John Lewis as we wanted a one stop shop for our new fitted kitchen. The designer came to see the kitchen and the building we were in (although he might has well not have come). The design took months to finalize and when I had many questions including about a 4 inch space on either side of the fridge it was because I didnt buy an integrated fridge it was my problem or a riser that stopped an inch short of the windowsill was the way it was fabricated. Likewise on the sink they sent a "dimensioned" plan with no identification of the model of the sink or its dimensions and when it arrived it looked like it was a bar sink and should have been in a kitchen half the size! The splashback was so ill fitting that the fitter suggested we just don't put it up! This was John Lewis own contractor!
We had the fitter manager (a JL employee) come out who agreed the sink looked small and suggested it could be fairly easily be fixed but when it went back to the company they said it was per the dimensions on the drawing and it was all they were going to do.
I have to say the one bright spot in the whole experience was the Case manager who really tried to do the right thing (changed out the fridge, got a new riser) but after over 13 months we have been told by the escalation care center that they are not prepared to do anything more (which is actually nothing except argue with us) after the initial fitting.
I would never recommend John Lewis Kitchens to anyone - they may be OK as a department store but the premium price is absolutely not worth it for the kitchen design or fitting.
Shambolic, Disappointing And Very Poor Attention To Detail
The product quality is good, but the design was flawed and needs rectifying
The fitters went off site with lots of work outstanding and some work of very poor quality that needs putting right.
We are 4 months in and suspect we have at least another month before all issues are resolved, if at all.
There is a total lack of customer care or commitment. Once you have paid, you might as well have used a bunch of sham artists.
We are having exactly the same issues. Our job started 4 months ago, and it has still not been finished. We have not been treated as a priority (as we would have expected when things go badly wrong), it’s just been a constant fight, and numerous emails, telephone calls and empty apologies.
Value For Money
Shocking From Start To Finish
I would second a lot of the reviews I've read there. My kitchen was supposed to be a simple 1 week job, it took 28 weeks in the end. There was absolutely no project management, things went wrong on numerous occasions (including the work surface being made the correct size a number of times) and the John Lewis team seemed completely unsympathetic. Caused a significant amount of stress and upset over 6 months. Final insult is an offer of less than 2% compensation for the inconvenience. I would highly recommend looking elsewhere for a new kitchen!!
Value For Money
I Would Avoid At All Costs
My review echo’s others on this site. Kitchen took thirty weeks instead of the three initially agreed. Poor quality product with many door replacements. Has only been finished a few months and now one of the door hinges has broken and door is falling off. Overall very poor communication and poor customer service. If you have been a John Lewis customer for many years as I have, don’t think that this service even remotely resembles the service you are used to from the stores.
Value For Money
Absolutely Terrible Experience
In my years of refurbishing using John Lewis Partnership for a new kitchen has been the absolute worst. All of it is untrue, there is no organisation, there is no project management, there is no quality control and there is zero customer service. The design started in December 2021 and to this date in April 2023 it is still not finished. They give you out sourced contractors who you have no idea where they come from or if they are qualified, We are now on our third contractor. The first one was diabolical, the second annoying and would not listen, god help me if this third one will finish things correctly. Please avoid using this dreadful service, John Lewis should be ashamed especially their chairwoman who obviously has not tried and tested this department. Never again.
Value For Money
Go Elsewhere - Hopeless Operation
The communication is simply dreadful. I have had two different and equally useless case managers since March 2022 dealing with my kitchen. It's approaching 12 months since I agreed to the kitchen and there remain simple but irritating fixes to be resolved. Despite all of the grief along the way, I never once received acknolwedgement, apology or compensation from JL.
They send out / fit damaged or faulty parts. Replacing them is a whole process in itself. I am tired and drained of this.
Timeline to date:
March 2022 - kitchen design agreed / order placed
June 2022 - original fit date
August 2022 - revised fit date following suggested additional plastering at additional cost
September 2022 - partially complete. Damaged/missing parts to be replaced.
October 2022 - incorrect replacement parts delivered and occupy hallspace.
January 9 2023 - JL advises the fitter will be back on this date
January 23 2023 - fitter gets in touch to finish job
January 25 2023 - fitter completes their job, finishing issues remain with alignment of hob and one plinth which they are unable to fix. Advised JL for the nth time that a shelf is still missing.
Feb 2023 - missing shelf arrives, significantly damaged.
Value For Money
Delays And Disorganisation
My advise would be to go elsewhere. I have always used and trusted John Lewis but the experience of having my kitchen replaced was one of delays, lost or undelivered items, piles of rubbish left in my flat for ages before the disposal people came.
The system does not work, design is fine, then you pay up front and from the moment the fitters come things go wrong. There is no one in charge and you cannot as the client manage things as it all happens miles away through a co-ordinator you never meet and who never visits the site. The details are boring but on the third day all the units and appliances were meant to come. The disposal people had not removed the waste so there was no space. All the appliances were put on lorries that day for delivery and had to be sent back. the deliveries were then delayed for a week then arrived with things missing. It just went on from there. a month later, no kitchen , my home upside down and more takeaway food.
If you want a really stressful nightmare go to John Lewis! You pay up front and once they have all the money you have no redress. The system needs a complete overhaul it just doesn't work.
Q&A
There are no questions yet. Be the first to ask a question.